Lange hatte ich keine Zeit, um mich mit Funk-Themen zu beschäftigen. Aber vor einiger Zeit erinnerte ich mich wieder an meinen RTL-SDR-Dongle. Diesen kramte ich aus seinem ruhigen Plätzchen in der hintersten Ecke der Schreibtisch-Schublade hervor und machte einige RX-Experimente mittels Nooelec-Upconverter (diesen hatte ich unbenutzt seit über einem Jahr in der Werkstatt liegen). Was ich schnell zeigte: Ein nicht wirklich berauschender Signalpegel im HF-Bereich. Offensichtlich dämpft der Upconverter so ordentlich, dass nur wenige (Radio)-Station zu hören waren – von AFu ganz zu schwiegen – obwohl ich das RX-Setup an einem sonst ordentlich performenden Dipol betrieb.
Daher entschloss ich mich, mittels vorgeschaltetem LNA dem Signal auf die Beine zu helfen. Im Netz fand ich nach einigen Recherchen den sog. LNA4HF, ein speziell für den HF-Bereich ausgelegter SDR-Upconverter-Verstärker. Fertig bestückt und inkl. Porto für 20,- Euro bestellte ich gleich einen. Wie ich feststellte bietet der kroatische OM 9A4QV, der den LNA entwickelt hat und nun produziert und weltweit über das Internet direkt vertreibt, auch einen LNA für den Frequenz-Bereich über 30 MHz an. Diesen LNA4ALL genannten Verstärker bestellte ich ebenfalls gleich mit.
Nach ein paar Tagen trudelten die beiden kleinen Platinchen per Post ein. Ein erster Funktionsaufbau – und -test beider LNA’s verlief erfolgreich. Wer zur Performance dazu mehr erfahren will, der findet HIER einen entsprechenden Artikel.
Doch die offene Elektronik störte mich. Also konstruierte ich kurzer Hand sowohl für die beiden LNA’s als auch für den Upconverter passende Kunststoffgehäuse, die ich anschließend von einem 3D-Druck-Service ausdrucken lies, da ich zu dem Zeitpunkt noch keinen eigenen 3D-Drucker in der Bastelkammer hatte.
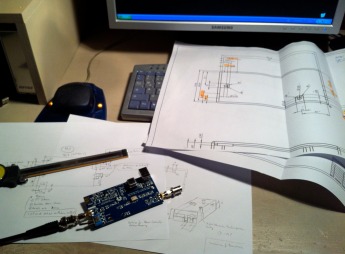
Nach Handskizzen und erster Konstruktion werden vor dem Druck noch einmal alle relevanten Maße kontrolliert.
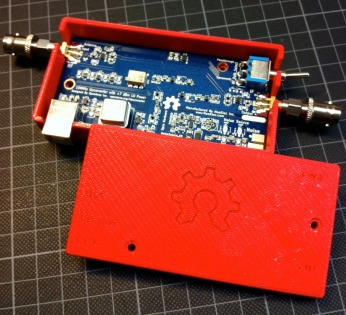
Upconverter-Gehäuse in geöffneten Zustand. Die Innnenseiten des Gehäuses wurde später noch mit Aluminium-Tape beklebt, um eine HF-Schirmung sicherzustellen.
Im LNA-Gehäuse habe ich beide Verstärker nebeneinander angeordnet. Über einen einfachen Kippschalter wird entweder der eine oder aber der andere LNA mit Spannung versorgt, die von der seitlich angeordneten DC-Buchse kommt.
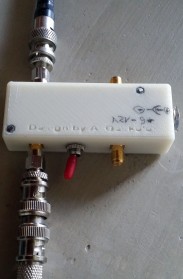
Die Unterseite des LNA-Gehäuses. Die beiden LNA’s sind parallel montiert. Mit dem Kippschalter wird die Spannungsversorgung auf den jeweils verwendeten LNA geschaltet.
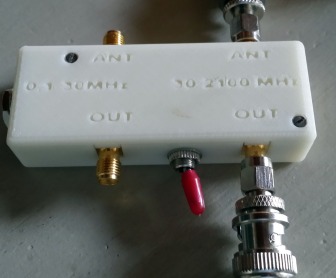
Die Vorderseite – links ist der LNA4HF und rechts der LNA4All montiert. Die Innenseiten des Gehäuses sind mit Aluminium-Tape beklebt, um eine HF_Schirmung zu haben.
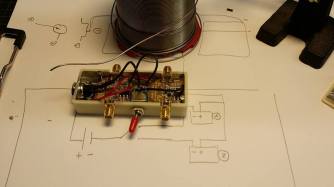
Die beiden LNA’s sind nebeneinander angeordnet. Dazwischen ein Kippschalter, um die Spannungsversorgung auf den jeweils genutzten LNA zu schalten. Links ist die DC-Buchse zu erkennen.
Zu meiner großen Freude zeigten beide Gehäuse eine wirklich gute Passform. Ich musste lediglich die Stützstrukturen entfernen und mit einem Cutter kleine Unebenheiten an den Gehäusedurchbrechungen leicht abschaben. Um die Gehäuse entsprechend abzuschirmen habe ich auf Aluminium-Tape zurückgegriffen, mit welchem ich die Gehäuse von innen beklebte.
Für Nachbaubegeisterte habe ich hier die Druckdaten (STL) für das Upconverter-Gehäuse und das LNA-Gehäuse zum download bei thingiverse abgelegt.
Zum Nachbau der Gehäuse sind folgende Materialien nötig:
4x M3-Schrauben & Muttern
4 Druckteile: Ober- und Unterteile der beiden Gehäuse
1x SMA-Adapter
Aluminium-Klebeband
2x Kippschalter
1x DC-Einbaubuchse