In den vergangene Tagen habe ich in der Werkstatt etwas weiter gemacht. Nachdem ich versucht hatte, das Griffstück der zuschießenden Maschinenkarabiner-Version aus Stahlblech zu biegen, die Ergebnisse mich aber nicht überzeugten habe ich umgeplant. Nun fertige ich ein Ur-Modell der Griff-Baugruppe an, die ich später für die Herstellung einer Gussform nutzen will. In dieser möchte ich dann die Griff-Baugruppe aus einem verstärkten Resin herstellen. Dabei will ich dann versuchen, den Harz mit Glasfaser-Mehl zu verstärken.
Nun ging es in den letzten Tage also darum, ein Urmodell herzustellen. Die Idee ist, die äusseren Flächen des Griffstücks aus Polystyrol-Platten zu fräsen und den Kern des Griffs aus MDF-Plattenmaterial (19mm) aus dem vollen zu fräsen.
Nach dem ich die PS-Teile (Ober- und Unterteile der linken und rechten Seite) fertig hatte, musste die CNC-Fräse mal zeigen, wie Sie mit MDF zurecht kommt. Dazu habe ich erstmals einen 6mm Fräser eingesetzt – das Ergebnis hat mich überzeugt.
Hier nun einige Impressionen der vergangen Tage Bastelkammer-Arbeit:
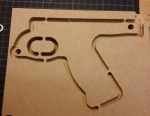
Gefräster Griffkern für Mockup Urmodell des Griffstücks für den zusch. MKb42(H).

Griffkern wird eingepasst.

Aufnahme-Öffnung, um später den Abzug montieren zu können.

Erste Anprobe des Urmodells…

Alle gefrästen Teile für die Herstellung des Urmodells (zMKb42(H))

Bauteile des Griff-Ur-Modells, v.l.n.r.: rechte Seitenteil (oben und unten), Griffkern aus MDF, linke Seitenteil (oben und unten).

Verkleben der Polystyrol-Seitenteile mit dem Griffkern – zusammenpressen mittels Schraubzwingen.
So, bald geht es weiter – sowohl mit dem Bau des Urmodells, als auch mit der 3D-Konstruktion der übrigen Bauteile…
Horrido und stay tuned…